1. Glossiness of binder
The main components of ink are binder and pigment. The glossiness of binder is the main factor that determines whether the ink print can produce gloss. The early ink binder was made of vegetable oils such as linseed oil, tung oil, and catalpa oil. The smoothness of the surface of the print after conjunctiva was not high, and it could only present a fatty film surface, which formed diffuse reflection of the incident light, and the glossiness of the print was poor. Now, the binder of ink is mainly composed of resin. The surface of the print after conjunctiva is smooth, and the diffuse reflection of the incident light is reduced, so the gloss of the print is several times higher than that of oil ink.
2. Glossiness of pigment
The first factor that affects the gloss of the pigment is the fineness. Ink made of uniform and fine pigment particles can make the conjunctiva surface of the print smooth, prevent the diffuse reflection of the incident light, and make the print reflect gloss. The particle fineness of high-grade ink is between 3-4μm, and the particle fineness of general ink is between 8-10μm. The finer the particles, the more conducive it is for the print to produce gloss.
The second is the transparency of the ink. After the ink with high transparency forms the ink film color layer, part of the incident light is reflected by the surface of the ink film, and the other part reaches the surface of the paper and is reflected again, forming two color filters. This complex reflection mechanism enriches the color effect, while the color film formed by the opaque pigment has a gloss only obtained by surface reflection, and the gloss effect is definitely not as good as transparent ink.
3. The influence of ink characteristics on gloss
Once the ink is manufactured, the anti-coagulation, leveling, and drying properties of its printability also affect the gloss of the print.
① The coagulation of ink on the rubber roller is a complex physical and chemical phenomenon. Whether it is an electromagnetic effect or an oxidation reaction remains to be determined by scientists after further research. The poor anti-coagulation of domestic inks causes the ink on the rubber roller to coagulate and become coarse during the printing process, which not only affects the clarity of the dots and the expression of the layers, but also makes the surface of the imprinted film layer rough, affecting the gloss.
② After the ink is printed on the paper, the print should also have the characteristics of self-leveling during the drying process. The better the leveling effect of the imprinted ink layer, the glossier the finished product.
③ There are three ways to dry the print: penetration drying, volatile drying, and oxidation film drying. Among them, penetration drying has a greater impact on the gloss of the print. When the ink is transferred to the paper, the solvent part of the binder penetrates into the paper at a faster speed. At the same time, the coating and paper fibers absorb the binder. The rougher the paper, the stronger its absorption capacity for the binder. Before the oxidation film drying, the binder is mostly absorbed by the paper fibers, and the remaining small part of the binder and pigment particles adhere to the surface of the paper, making the product dull.
For more details and information, welcome to send requirement to sales@paiouscreenmesh.com, or you can reach us at Tel/Whatsapp/Wechat: +86 19932893768
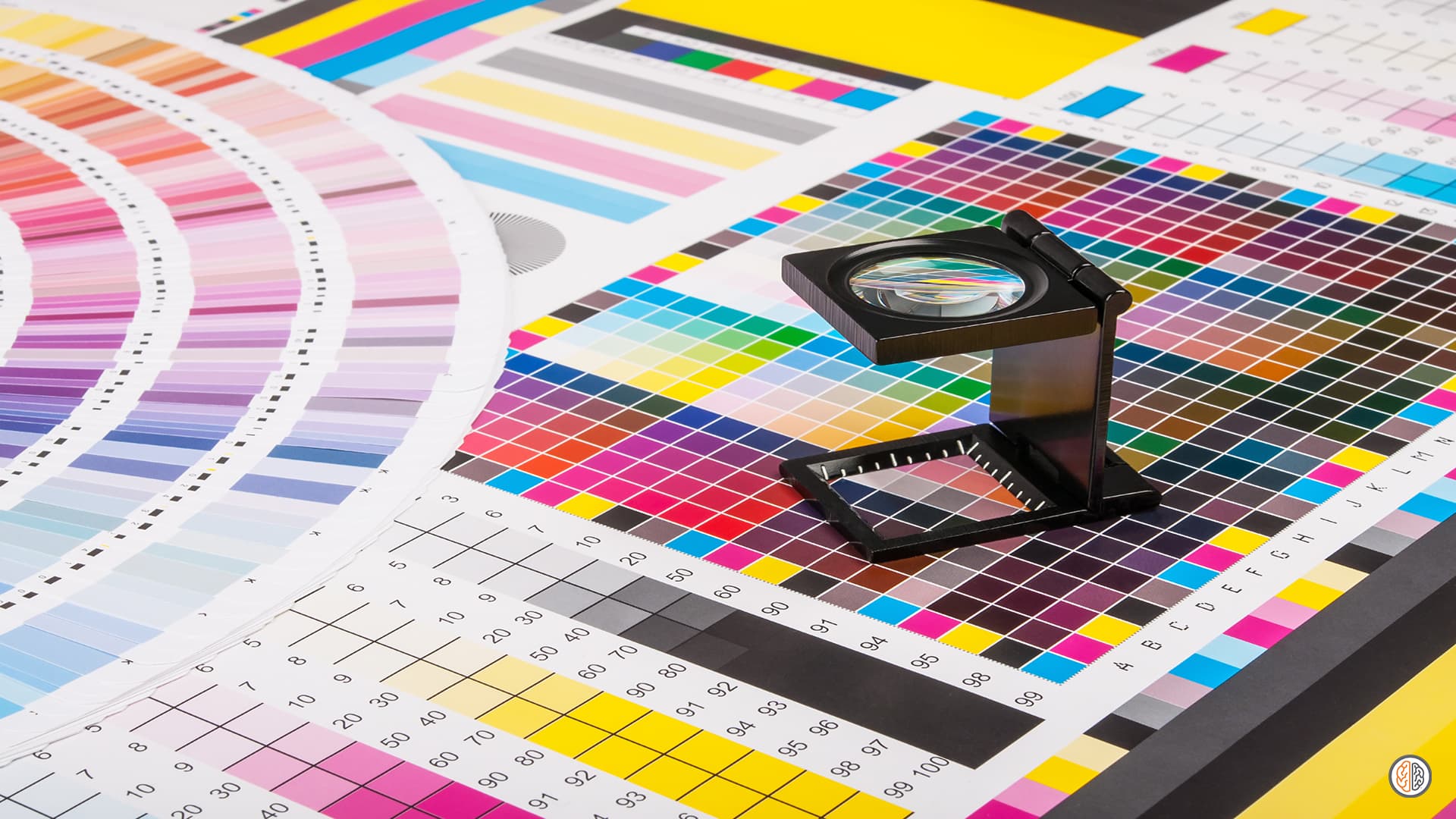